From the idea to construction
Component development is the basis of a successful project. In close cooperation with our customers, we develop innovative polymer moulded parts and components as part of a new development, a black box design or optimisation. Our developments are process-orientated and function-orientated. The concepts developed in this way fulfil customer requirements and can be successfully transferred to series production.
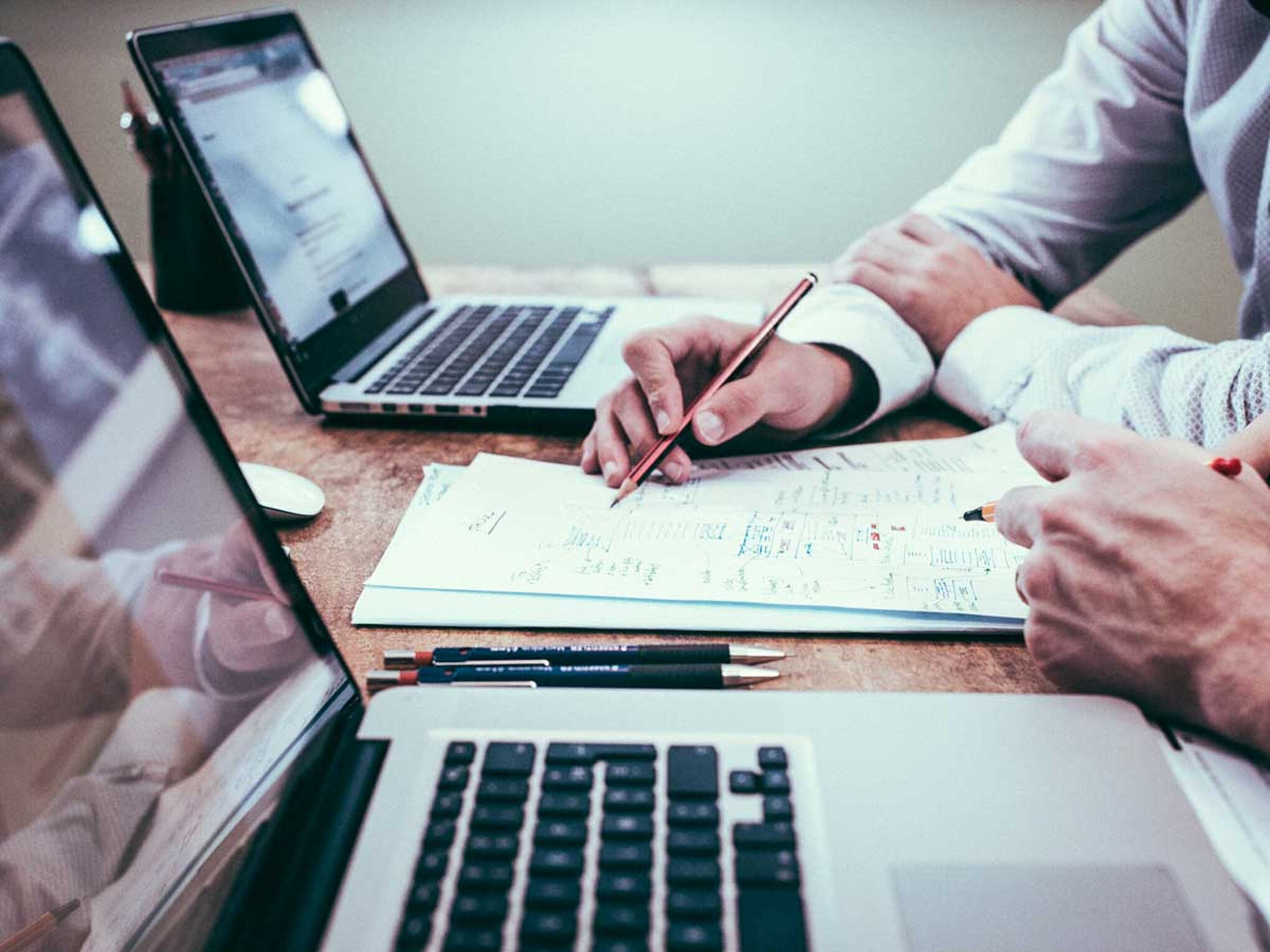
Advanced Development
The first step towards the finished product is advanced development.
We use creativity techniques and structured development methods, such as TRIZ, to develop new ideas. In doing so, we pay particular attention to the requirements of our customers and the market with the help of profitability analyses and prototyping.
Metal substitution, functional integration and cost-saving potential are core competences of our advanced developments.
Material development
Our focus in "Fluid Engineering" is on media-carrying applications. Have you ever asked your supplier of thermoplastics what their polymer can still do after 15 years in the field? Do you know the degree of ageing? Ask us! We have invested in our own versatile "Xbody" test body, installed a water laboratory and developed a special ageing process. We know the degradation of the decisive polymers and thus the characteristic values for the realistic FEM simulation. We go to the limit!
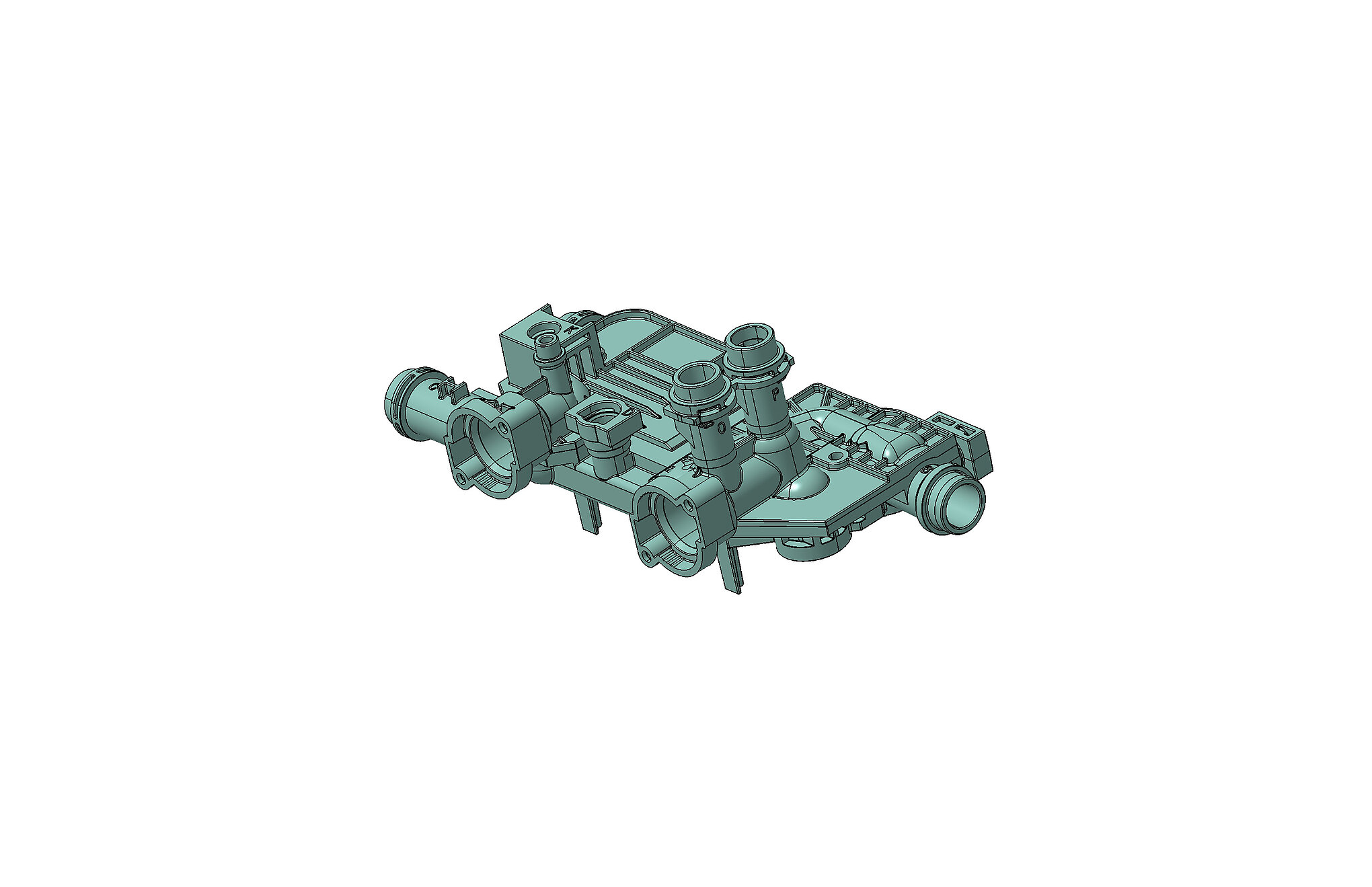
Concept and construction
The resulting ideas and concepts are realised in three-dimensional geometries. Our customers' requirements for the product and various specifications are incorporated into the design. Particularly important here is the combination of design and function, which also includes the tooling, production and assembly requirements of a sophisticated component. Matching the fixtures to the corresponding components and assemblies ensures a flawless process and an optimum result. Synergies are created through the interaction of concept studies, article design, assembly design, design of gauges and fixtures, equipment design, test equipment design and reverse engineering.
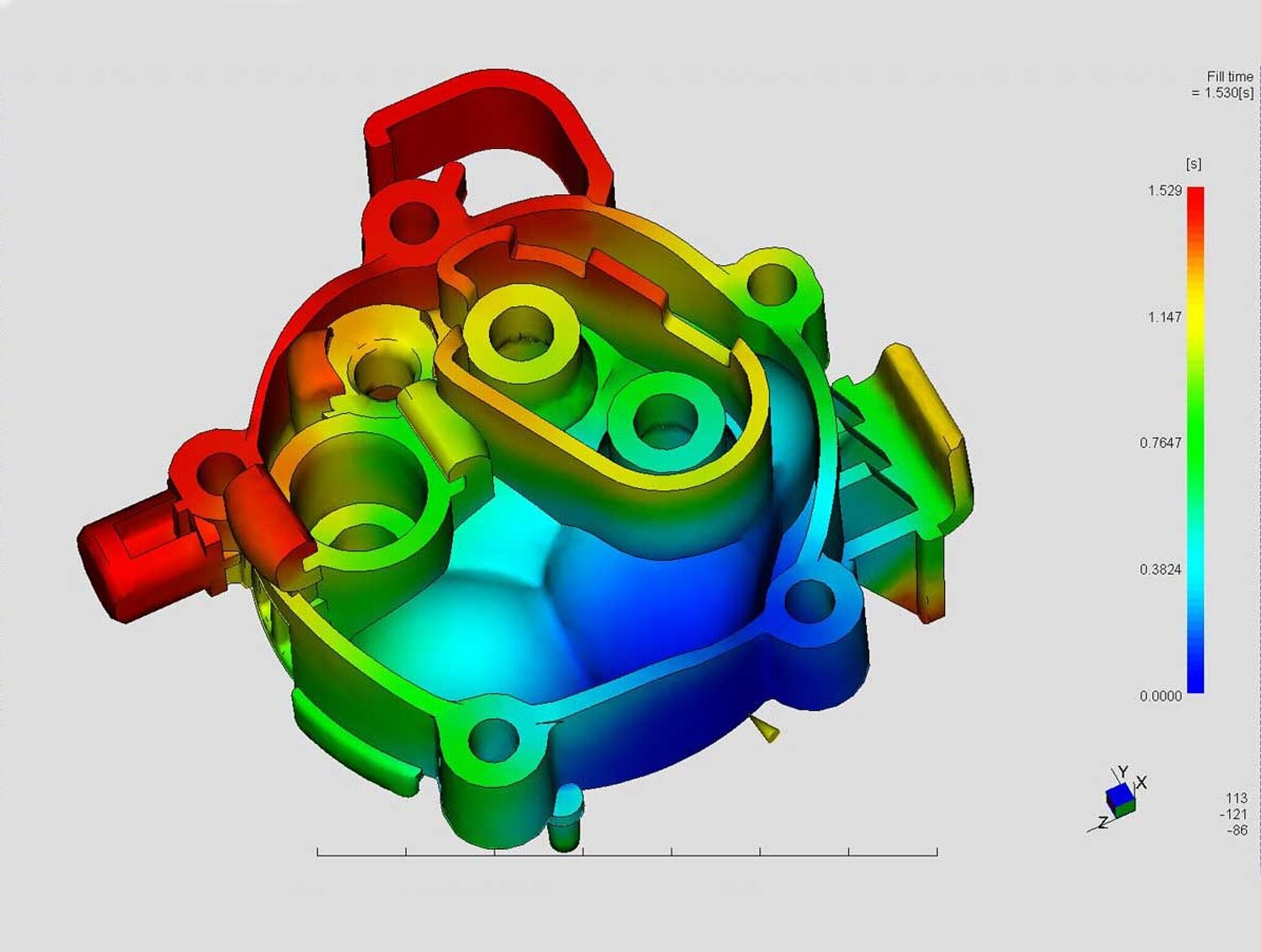
Simulation
The development of systems is characterised by a high degree of complexity. Even in the early stages of development, simulations can be used to make reliable predictions about production and component behaviour.
Virtual validation takes place via
- Process simulation
- Finite element calculation (FEM)
- Flow simulation (CFD)
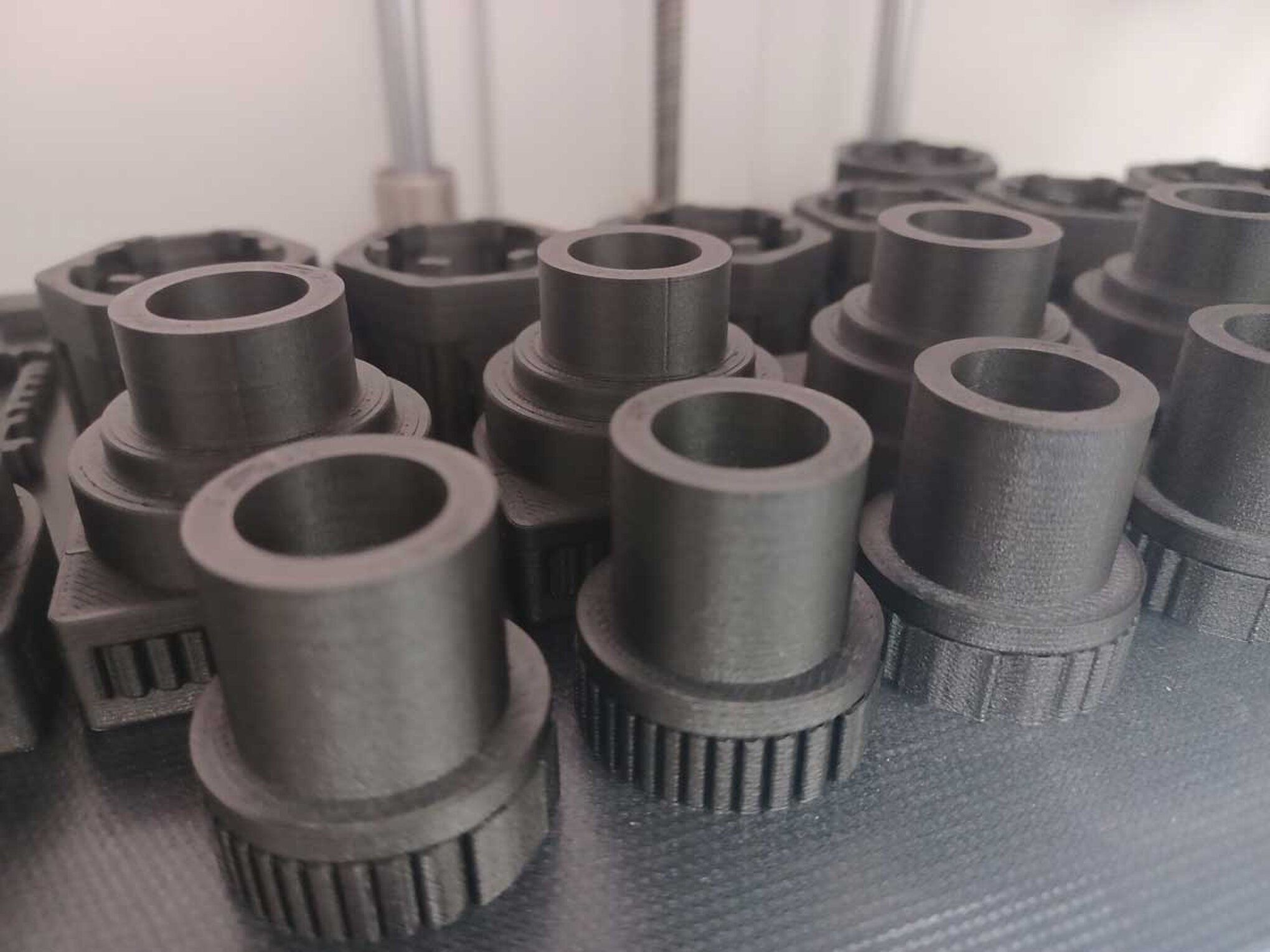
Rapid Prototyping
Rapid prototyping allows 3D models of the components to be produced. The 3D printing process supports product development both in the presentation of the design to the customer and in concept and functional testing. Optimisations to the design can thus be made more quickly. All common rapid prototyping processes are used, from the smallest to the largest component geometry.
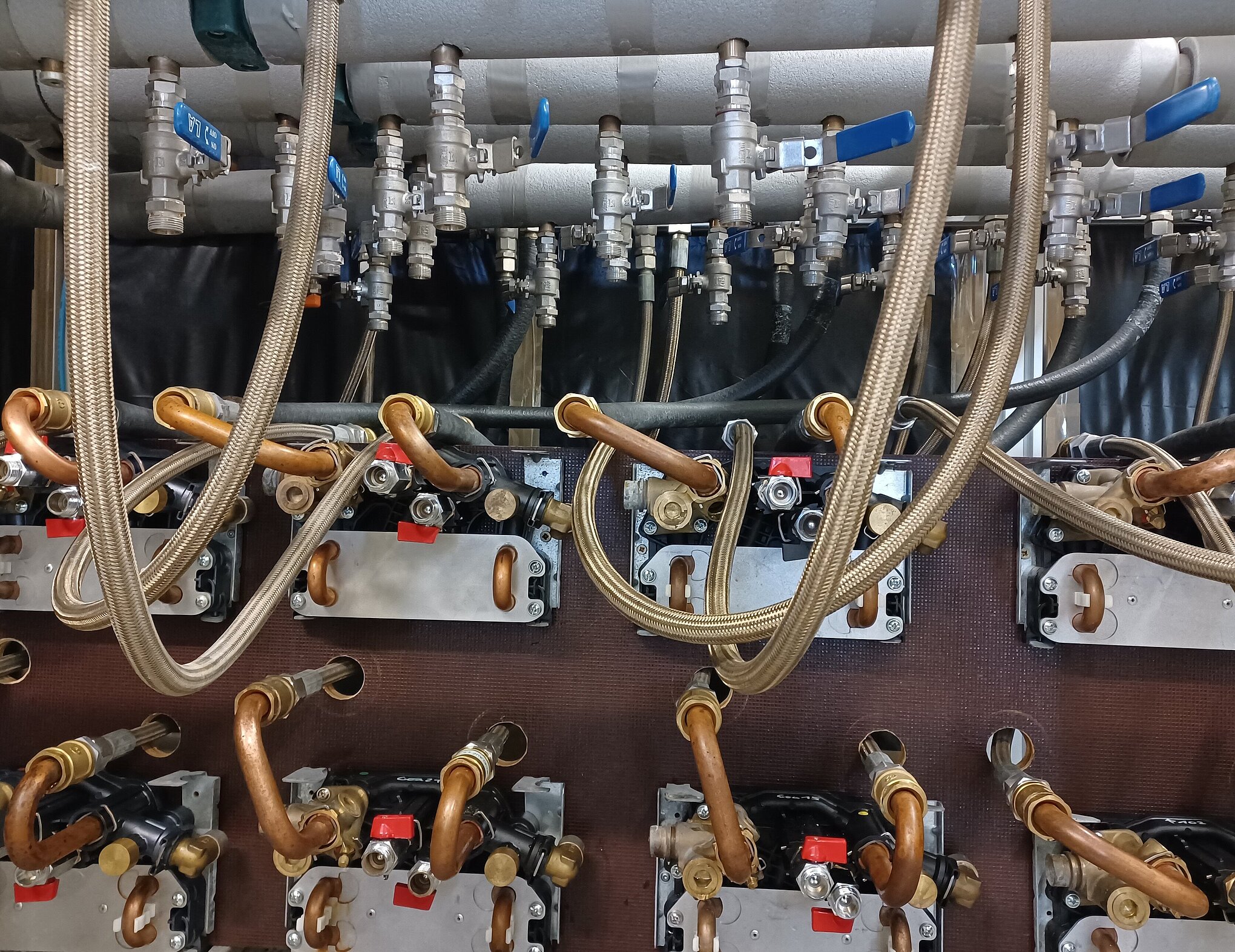
Testing
The testing of our components rounds off the system development process. We have a wide range of testing options at our disposal. It is possible to map standardised test sequences as well as a customer-specific test setup.
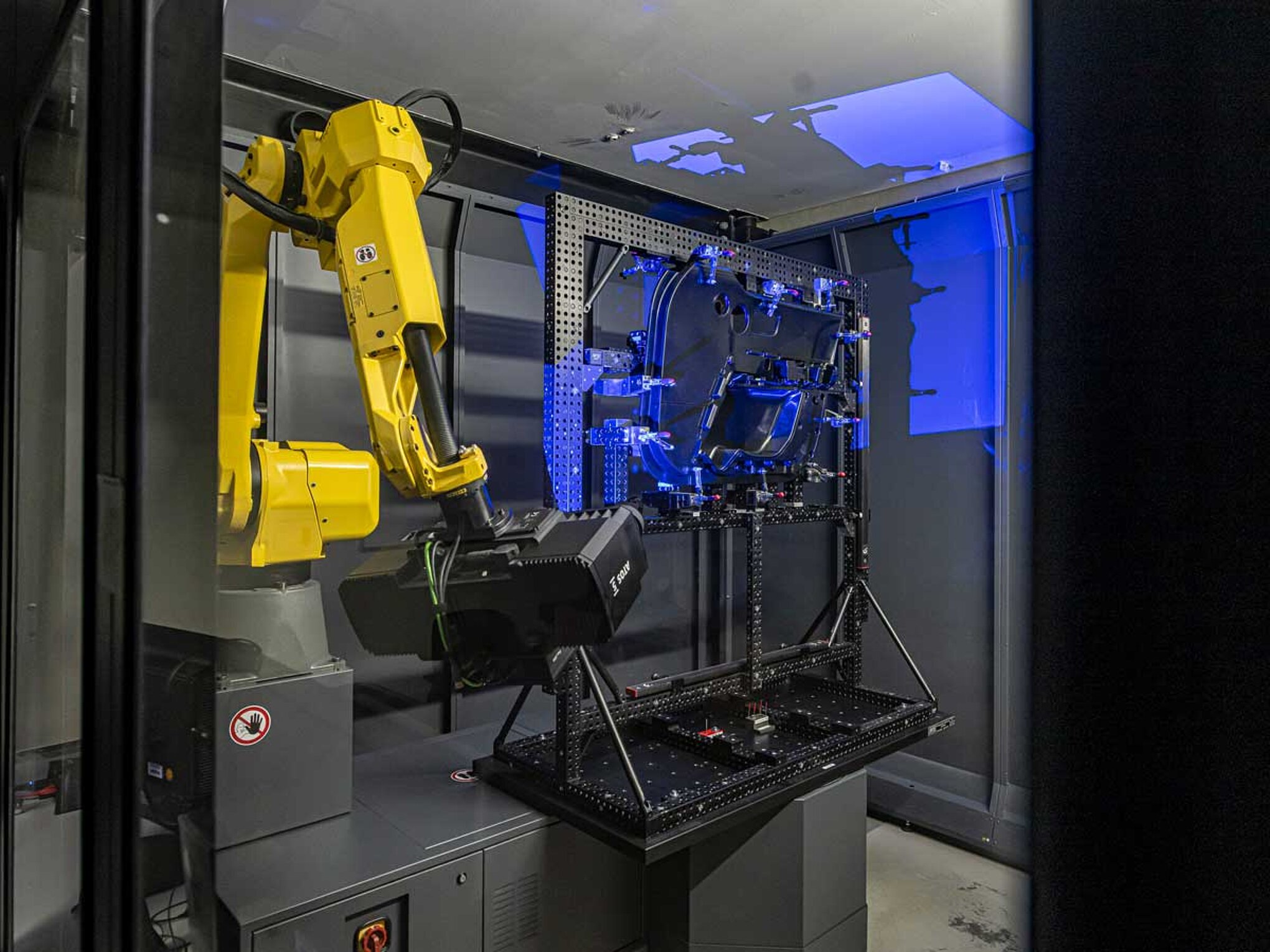
Measurement and scanning
Using the latest methods, such as computer tomography or 3D scanning, 2D, 3D and free-form components are precisely measured and analysed. The test reports are created in accordance with standards (e.g. VDA or IATF 16949) or customer-specific requirements.
Please contact us!
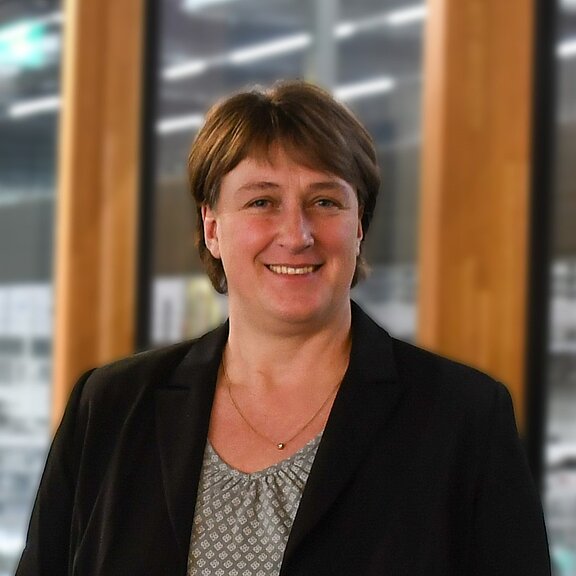